Engineers are more than mathematicians and mechanics. They're innovators, inventors and problem-solvers. For the past year, senior engineering majors have been working on their capstones that address some of the world's problems. These students will present their final projects in the last month of school at the Shiley showcase, and in some instances, they'll give their projects away to those who can use them.
Capstone groups, which consist of three to six students, were assigned last spring after each engineering major ranked the general field they were interested in. Once the groups were formed, each group received their specific assignment and a sponsor, which is a professional, an organization or a professor that provides funds for the project and mentors the students. Groups use these funds to buy materials, research and travel to different expos and showcases.
For their assignments, students work together to solve issues ranging from unsafe cooking mechanisms for women in Ghana to inaccessible mobile toys for kids with disabilities. After a year of working to resolve these issues, the groups are almost done and will present their capstones on Founders’ Day or at the Shiley Showcase on the Friday of dead week.
There are many fascinating projects that can be seen at the Shiley Showcase. Here are just three projects that capstone groups have been working on.
Go Baby Go
Senior mechanical engineering majors Jacob Wolwowicz, Parker Elliot, Ally Fox, Philipp Holzmann and Laura Pickering have been working alongside the Oregon branch of Go Baby Go, a national non-profit that modifies toy cars for children with disabilities. As a group, their goal is to take electric cars made for children (Power Wheels) and make them more accessible for children that are only able to move their head.
The car will be operated entirely by head movements. For the past year, the group has been designing modifications for a Dodge Ram Power Wheel Car, which was provided by Go Baby Go. They re-wired the wheels so that the car turns and moves forward when the child presses buttons with their head.
“I love it,” Pickering said. “It has been the greatest project I could ever imagine. It’s a really cool company. Kids that are younger that don’t have the ability to move around, they miss a huge developmental stage. Powered wheelchairs don’t come in sizes small enough, and they’re really expensive. So, Go Baby Go’s main focus to make it affordable to get their kids a range of exploration.”
One of the group’s goals for the project is to make their design easy for families to build themselves, so they bought most of their materials from an ordinary hardware store.
“No welding, nothing fancy like that,” Elliot said. “All of it’s PVC connections, a PVC structure to hold up the buttons. You have to order the circuits from online, but you can put them together yourself. The code we made, we’re just going to give (the families) so that they can just upload it to the same (circuit) board.”

The team built a structure out of PVC pipes that allows a child with limited mobility to push buttons with their head, pushing the car forward. Photo courtesy of Pickering.
Go Baby Go recently paired the group with a family that they can give the car to after they finish the project. There are two boys in the family. The younger one, six-year-old Reid, has very limited movement in his arms and legs and uses a powered wheelchair. The car is big enough for both of the boys to sit in, even though Reid will be the one controlling it.
“They've been involved with Go Baby Go and he has driven a smaller car before, but since he is now older and a bit bigger, Go Baby Go has fewer options for him,” Pickering said. “Reid is super excited about driving the car, we put him into the seat to make sure he fits well in it, and he could not stop smiling.”
Elliot got a job with the Go Baby Go team and will work on one of their committees after graduation, and will coordinate more projects with other schools and groups. Pickering will be working at Daimler, a company in Portland that builds pickup trucks. Wolwowicz is a five-year engineering student and will join the Oregon National Guard after graduation, where he will serve for six years. Fox will spend part of her summer volunteering in Africa.
Distal Limb Pressure Boot
When senior mechanical engineering major Nicholas Nelson called a plastic store, he hoped they could supply his group with some parts for their capstone project. But when he told the sales rep that the parts were for a distal limb pressure boot, the rep just yelled back “what?” This is a common reaction at first glance of this boot, Nelson said.
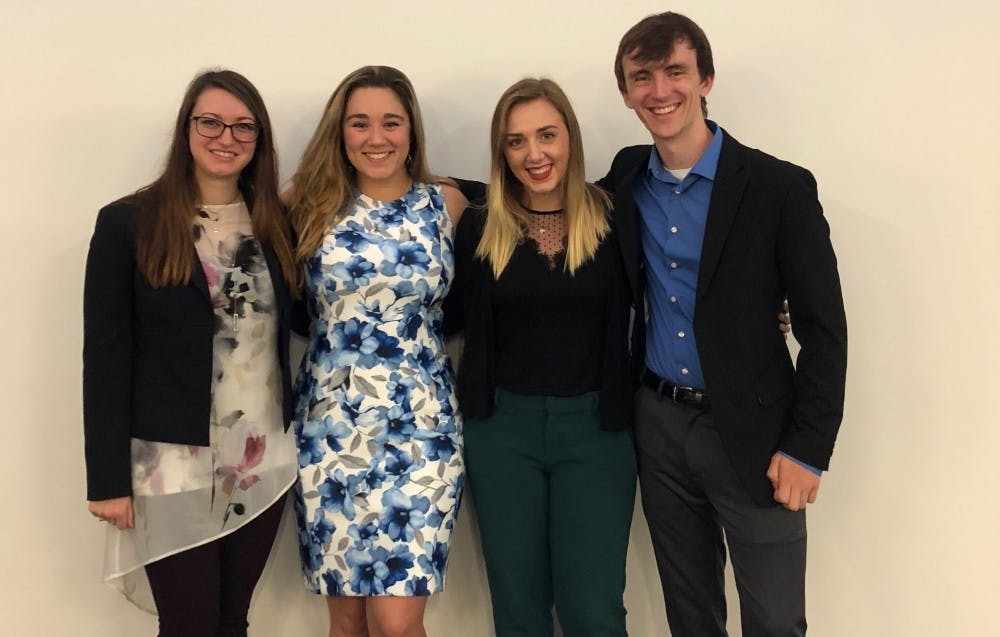
Left to right: Seniors Jenna Fortner, Olivia Beckham, Kiley Gersch and Nicholas Nelson. Photo courtesy of Gersch.
Nelson and seniors Olivia Beckham, Jenna Fortner and Kiley Gersch are building a therapeutic boot for people with lymphedema, a type of swelling that occurs when lymph builds up in a body’s soft tissues. Many of the current solutions for this disease make patients immobile, so the group’s main goal is to create a boot that reduces swelling but also allows patients to move around.

Seniors Jenna Fortner, Olivia Beckham, Kiley Gersch and Nicholas Nelson built a prototype of a distal limb pressure boot, which reduces swelling in the legs but still allows patients to move around. Photo courtesy of Gersch.
“Our design right now is creating a knee high sock, almost, that has really small inflatables inside of it,” Gersch said. “It’s called peristaltic inflation. Basically what it does is move in a chain, so it moves up the leg to redistribute the fluid.”
The team is sponsored by Dr. Nathan Kemalyan, a burn surgeon in Portland who works with geriatric patients. Kemalyan, who has worked with many UP engineering capstone projects, came up with idea and brought it to the group last April.
“I think (Dr. Kamalyan) really appreciates the creativity that comes out of undergrads with a little less experience, and, as a result, less routine in the practice of design,” Nelson said.
Making the boot mobile for patients has been challenging, the group said. They’ve had issues with keeping the inflatables contained inside the boot. If the inflatables expand simultaneously, there will be too much pressure and the patient will become immobile.
“We’ve never really worked with a leg wrapped in inflatables," Gersch said. “It’s usually dealing with a steel beam that’s bending.”
Although they are all mechanical engineers, the team all wanted to work on a capstone in the biomedical field. After graduation, Gersch will pursue her masters in biomedical engineering at Johns Hopkins in Baltimore next year. According to Gersch, Johns Hopkins was very impressed with the project and the amount of work Beckham, Fortner, Gersch and Nelson were able to complete with the amount of money and time they had, Gersch said. Fortner will be pursuing a masters in biomedical engineering at UP next year, and Nelson is looking for graduate school opportunities in mechanical engineering. Beckham will be an Inside Sales Engineer for Johnson Barrow Oregon.
Shea Roaster for Women in Ghana
Senior engineering majors Spencer Marcinko, Michael Roberts and Haley Meisburger are working with Burn Design Lab, a for-profit company that creates safer and more affordable cooking stoves for people living in poverty around the world.
For their assignment, Marcinko, Roberts and Meisburger are working to build a shea roaster for women in Ghana. Roasting shea nuts is a major source of income for women in Ghana as shea nuts are used to create shea butter, which is used in lotions and various products in the cosmetic industry. Currently, many of the women are roasting the nuts over an open flame, putting them in danger of lung damage and severe burns.
Meisburger is the president of UP’s Global Engineering club, and traveled to Ghana over spring break with the club to work on a sanitation project, where they built a machine that can turn human waste into methane. Although the trip was unrelated to the project, Meisburger felt like her group’s capstone was going to make a difference there.
“We were walking through a community and I just saw the open flame cooking everywhere,” Meisburger said. “It reinforced the project. I bought some shea butter while I was there!”

Seniors Spencer Marcinko, Michael Roberts and Haley Meisburger created a prototype of a shea nut roaster for women in Ghana. Photo courtesy of Meisburger.
The group has been working together to build a safer and more efficient device for these women. They built a prototype that the women can put on top of a fire to protect them from the fumes. The mechanism has a rotating drum that the shea nuts go into, allowing them to roast above the flames.
The team also created a “low-cost temperature sensor,” which shows the women if they need to add more wood to make the device hotter. There is also a “hopper,” a piece of metal that acts as a ramp, where the women can insert the nuts into the device without burning their hands.
In preparation for their project, the group took a tour of St. John’s Coffee Roasters in Portland. Many elements in coffee roasting machines have become a large part of their project, including a cooling bin for the shea nuts.
The group hopes that, when the project is finished, Burn Design Lab will implement their design into one of their machines and bring it Ghana.
After graduation, Roberts and Marcinko plan on entering the workforce, and Meisburger will work as a designer at Glumac. But for right now, their focus is on the impact their project could have.
“I think it’s a very important project,” Meisburger said. “It has a very strong human focus. It’s hard to imagine, but these women in Ghana are working over these flames for hours a day. And their health is very impacted by open flame cooking. Their lives are indefinitely changed by something as simple as a cooking device.”
Fiona O’Brien is a reporter at The Beacon. She can be reached at obrienf21@up.edu.